The key points of the design of sandwich thermal insulation wall panels and their energy performance
Energy-saving in building envelope structures
Ultra-low energy buildings refer to structures that adapt to climate characteristics and natural conditions, featuring highly insulated and airtight envelopes, employing fresh air heat recovery technology, and utilizing renewable energy sources to provide a comfortable indoor environment. The concept of ultra-low energy buildings is relatively mature in the cold Nordic countries. As illustrated below, the design of ultra-low energy houses should consider the following points:
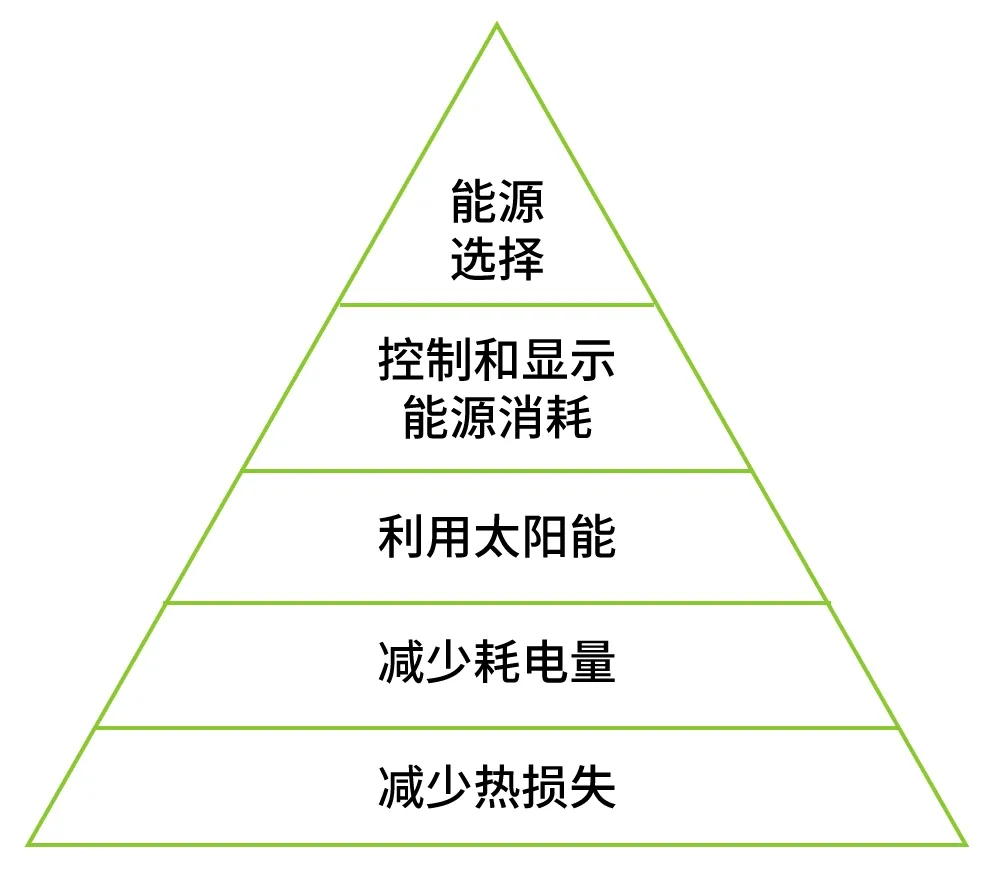
In Nordic countries, the efficiency of producing energy from solar power is very low, and the cost is high, making it a primary design principle in practical projects to minimize energy consumption. This is achieved through basic methods such as reducing thermal losses and air leakage in the building envelope, increasing insulation, avoiding thermal bridges, using materials with sufficiently low U-values (heat transfer coefficients) for doors and windows in walls, reducing the area of openings, and improving the airtightness of joints.
In buildings, the thermal loss of the building envelope is significant, and walls constitute a large portion of it. Therefore, reforming building walls and developing wall energy-saving technology are crucial aspects of building energy-saving technology. Developing external wall insulation technology and energy-saving materials is the main method of achieving building energy conservation. In the building envelope, insulated concrete composite wall panels (also known as “sandwich thermal insulation wall panels”) are increasingly used as the exterior skin of ultra-low energy houses. Typically, sandwich wall panels consist of inner and outer layers of concrete, a rigid insulation middle layer, and shear connectors between the inner and outer layers.
Combining structural performance and thermodynamic insulation properties
The practice of combining different material layers or substrates to form a sandwich composite material, achieving composite performance, can be traced back to before the 1960s. The greatest breakthrough for sandwich systems was in the aerospace field, particularly with the development of the Mosquito aircraft during World War II. After the 1960s, sandwich composite material technology began to be widely used in many fields such as automobile manufacturing, refrigeration equipment, shipbuilding, and construction.
In building materials, sandwich core wall panels, also known as precast concrete sandwich panels (PCSP), are considered an improvement over the solid slabs produced using the industrialized building system (IBS) method. They have significant thermal performance due to the insulation material created between the concrete layers and have been widely applied in civil engineering projects.
Compared to traditional building walls, precast concrete sandwich insulation walls effectively combine structural performance, thermodynamic insulation properties, and architectural decoration within a single wall panel. They are increasingly favored in engineering applications. Not only do they possess excellent fire resistance and durability, but the production process is also simple and suitable for industrialized production. During construction, there is no need to add additional insulation or decorative layers, which significantly shortens the construction period, increases construction speed, and reduces labor costs. The use of precast exterior walls can also achieve scaffold-free construction, reducing construction costs. These walls are gaining attention in building components and are gradually becoming the mainstream form of building walls.
For sandwich thermal insulation exterior wall panels in extremely cold regions, the typical thickness of the outer leaf protection layer is 60-80mm, with a B1 level intermediate layer of thermal insulation material measuring 200mm in thickness. In conjunction with innovative technologies such as coating-type waterproof vapor barrier/breathable technology, high airtightness treatment of panel joints, and thermal bridge-free embedded installation of external windows, it is possible to achieve high-performance thermal insulation, thermal bridge interruption, and moisture-proof integration in the exterior wall system. Notably, for insulation wall panels with a thickness exceeding 200mm, the use of truss-type shear connectors can meet the thermal engineering requirements of ultra-low energy buildings. In the cold Nordic regions, almost all ultra-low energy buildings employ truss-type shear connectors, and an increasing number of domestic projects are following this example.
Key factors — thermal conductivity of insulation materials, thermal bridges in connectors
In sandwich thermal insulation walls, connectors are typically placed between the inner and outer leaf wall panels, structurally linking the wall panels and insulation layer, and bearing the shear force between the two concrete wall panels. Moreover, the performance and arrangement of the shear connectors directly affect the thermodynamic performance of the entire sandwich thermal insulation wall panel. To avoid the thermal bridge effect at the connection points between the connectors and the wall, the connectors themselves should have a low thermal conductivity, good corrosion resistance, and durability, as well as a thermal expansion coefficient close to that of the wall panels to allow for relative sliding between the connectors and the wall panels. For wall panels using truss-type shear connectors, the only thermal bridge is the truss itself that connects the sandwich components, making it easier to arrange the connectors reasonably to avoid thermal bridges.
Overall, the sandwich thermal insulation wall panel form can meet the thermal engineering requirements of ultra-low energy buildings in regions with severe cold or hot summers and cold winters, fulfilling the prerequisites for their large-scale promotion and use.
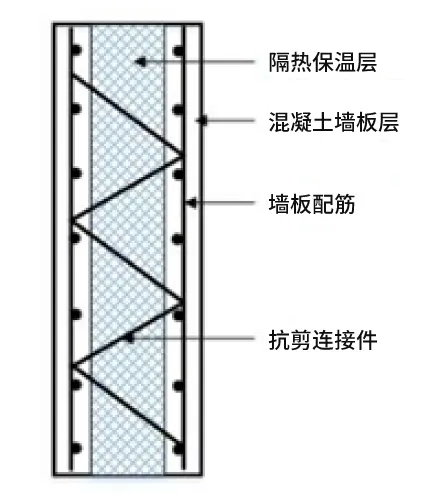
Additionally, the airtightness of the joints between structures and components should be given special attention from the early stages of design. Figure-2 shows a residential project in Finland where multi-layer single-component polyurethane foam material is used to seal the joints at the corner of the wall. The use of Peikko PVL® steel wire rope connection rings makes the connection of precast walls simple and feasible. China’s “Passive Ultra-Low Energy Building Technical Manual (Trial) (Residential Buildings)” also sets requirements for the airtightness of passive houses, and currently, the airtightness of the building envelope can be tested using the blower door method.
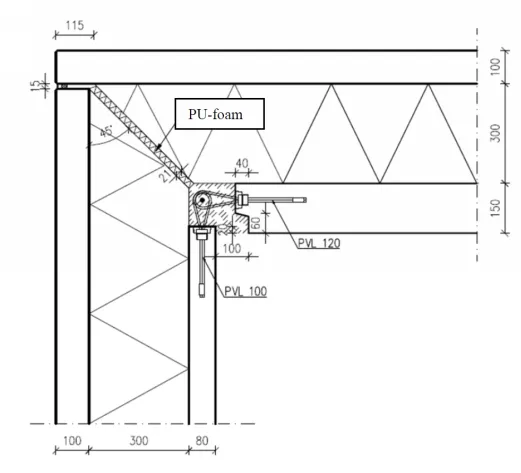
The table below shows the relationship between the thickness of the insulation board and its thermal conductivity function, as well as the impact of different sandwich insulation board connectors on the thermal conductivity coefficient.
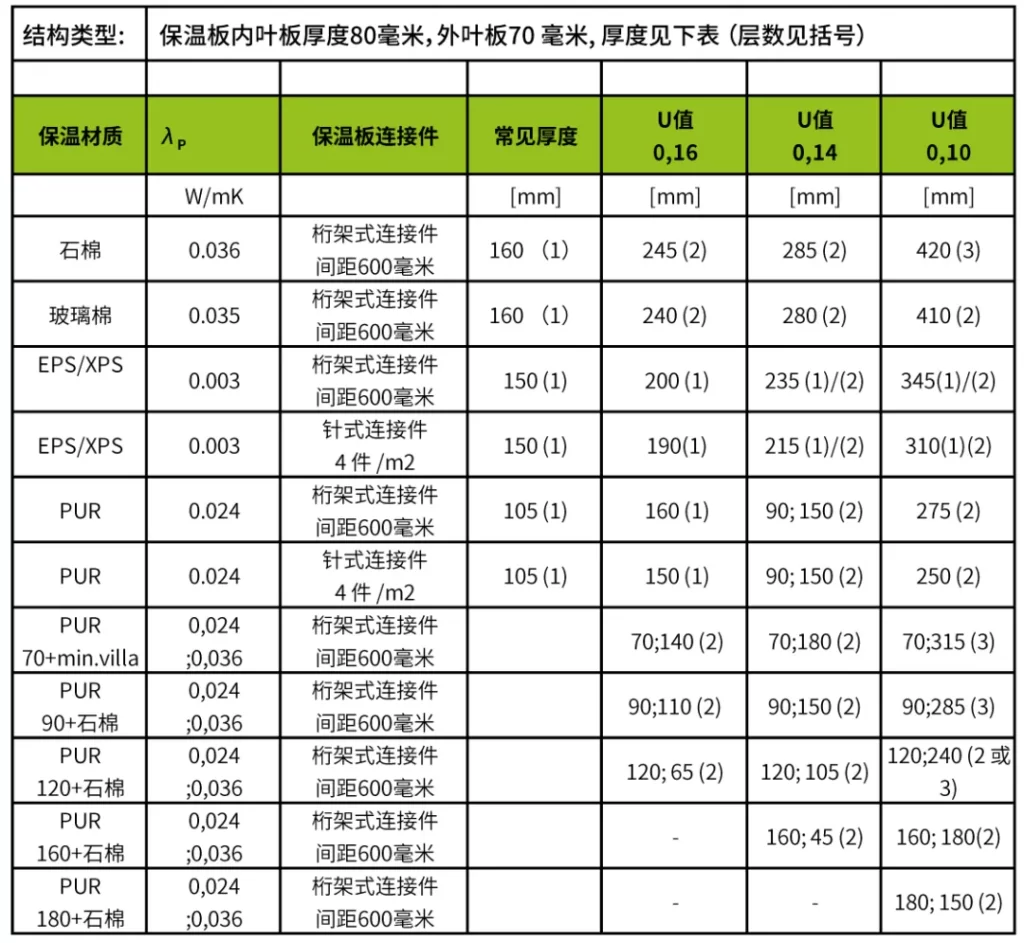
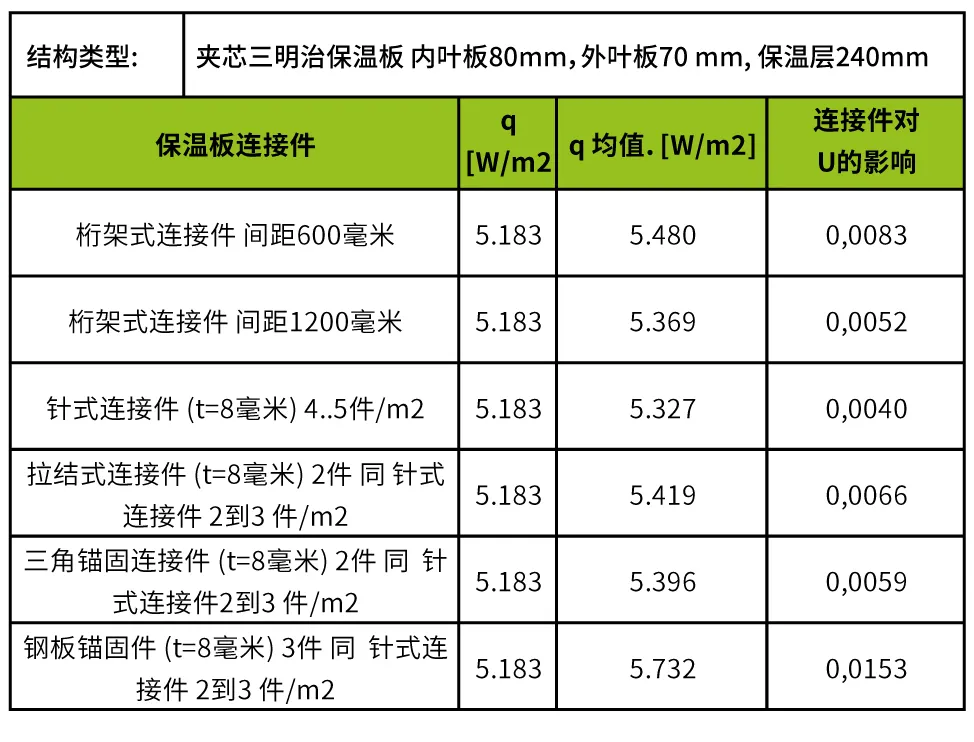